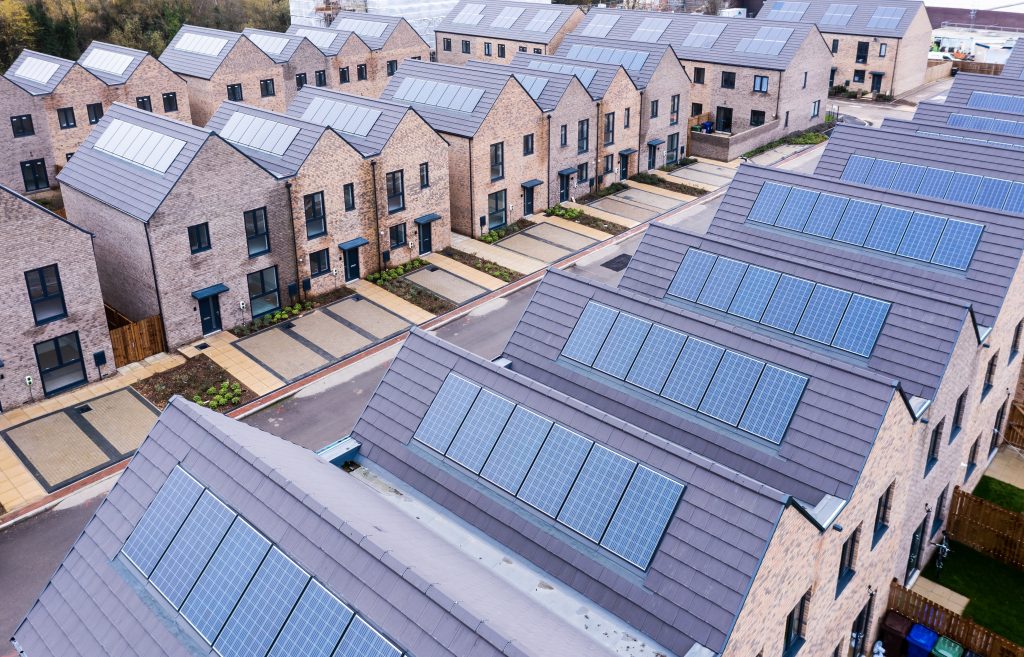
Tackling the housing crisis: Taking a closer look at challenges in delivering modular housing
Suzanne Peters, Jonatan Pinkse, Graham Winch
It is hard to miss it in the headlines these days: the UK is facing a housing crisis. This is not news. The country has struggled to reach housing targets for decades and there is no solution in sight. Indeed, with labour shortages, higher standards, inflation, supply issues, and important sustainability targets, it’s perhaps never been more difficult.
In light of these challenges, our team undertook research to investigate the productivity challenges in UK housing construction. The research has been published in an Insights Paper from The Productivity Institute: Driving change in UK housing construction: a Sisyphean task? The paper illustrates industry perceptions of the challenges and identification of the key issues. Importantly, the report makes several recommendations to support the sector.
Is “modular” part of the solution?
This research focuses on what the industry refers to as “Category 1” of so-called Modern Methods of Construction (MMC). For those outside of the industry, the category might be more commonly known as modular homes. These homes are largely built in a factory environment with the 3D modules then transported to a building site for assembly and completion. There are many preconceptions in the market about this method – some positive, some negative – but many in the industry agree that this is the most scalable and efficient approach. It represents an opportunity to improve productivity in the sector – producing more quality homes at pace – and offers important benefits in terms of sustainability (more precision, less waste), more efficient use of skilled labour (factory production lends itself to more flexibility in the skills required), and potentially safer methods that are well-supported in the controlled environment of a manufacturing facility.
Challenges are evident and complex
Despite its potential, these methods have struggled to gain traction in the UK. Indeed, high-profile failures of highly capitalised firms – including Ilke Homes and Legal & General Modular Homes – have raised concerns about the viability and dependability of this method. If you want to build homes, can you rely on this method to get to the finish line? The reality is that these businesses have failed but there are opportunities to improve outcomes. Our report provides details about the context of the industry and presents five key issues that have been identified as barriers:
1. The labour market requires new skills to meet the unique needs offsite approaches bring to the fore. Traditional methods of onsite construction have little in common with the manufacturing of homes in a factory environment. Offsite has specific needs and precise methods that are distinct from traditional methods and there is almost no margin for error or variance from the plan.
2. Projects must better accommodate the unique aspects of combining onsite and offsite methods. The particularities of both onsite and offsite methods also prove problematic when a factory-produced home is brought to a more traditional construction site for installation. Without careful coordination, communication and accommodations, there are bound to be issues when offsite components arrive onsite for completion.
3. Land use approvals are a massive challenge for the industry. Receiving government approval for new developments and housing plans is a difficult, expensive, and unpredictable process. This is particularly true for advanced methods of construction, such as modular homes, which vary from traditional proposals and can face more challenges in gaining approval.
4. The desire for flexibility limits productivity growth. Local planning authorities and individual home buyers tend to want unique designs to suit their preferences. Significant productivity gains come from scale and repeatable methods, which are challenging when the market demands are diverse. With the current approach, this limits the demand for products that are most likely to deliver productivity improvements, which limits the ability to deliver more quality homes faster.
5. The industry is not incentivised to change. Methods and processes are deeply engrained in a system where multiple players are needed to collaborate on the delivery of homes. Changes to the approach require the support of many, and making changes is typically quite complex and expensive. Compounding matters, trying new approaches can be fraught with risk. Each of these make changes extremely difficult to implement.
Opportunities to support the sector
These factors hold back new homes construction broadly speaking but are particularly problematic for Category 1 methods. Three avenues for potential improvements are presented as opportunities for government to help ensure greater successes for the sector:
1. Drive demand creation for MMC. Government can go further to incentivise builders to use MMC and drive change in the sector. Clear and actionable forward-looking policies and plans, ideally paired with positive financial levers, will help to move the industry forward.
2. Deliver an MMC-oriented skills agenda. To support the unique needs of offsite methods and the inevitable integration with onsite work, teams need to understand the intricacies of bringing these two methods together on a build site, and the coordination must happen early and often. There is little room for variances from the plan and missteps are expensive and time consuming.
3. Ensure efficient and pragmatic government approvals. To speed up progress and minimise risks for all parties, development and planning approvals need to be more predictable and timelier. Approvals can currently take years for homes that can be built in months – this needs to be addressed.
Improvements in this space would result in more quality homes being built at a faster pace than with traditional methods. That means more families in improved living situations, faster. It is vital that the industry – Category 1 and other methods – will be provided with improved conditions for success. The nation is burdened by an insufficient supply of homes that affects far too many people including those with a low income and those in more vulnerable situations.
Our research has just begun, and we are broadening our scope to other aspects of MMC and avenues to support the UK in reaching its housing targets. There are many opportunities to accelerate the delivery of quality homes, but the issues are complex and difficult for industry to solve without government support and objective research into the many challenges faced by the various key players. It is vital work and time for all to benefit from real progress that will improve outcomes and give individuals and families much-needed homes to move into.
For a more detailed discussion of the context, issues and recommendations, the full report can be found here with other new research from The Productivity Institute.
Alliance Manchester Business School Research Team: Suzanne Peters*, Jonatan Pinkse*, Graham Winch. This research was funded by The Productivity Institute through the support of UK Research and Innovation (UKRI) and the Economic and Social Research Council.
*Manchester Institute of Innovation Research
0 Comments